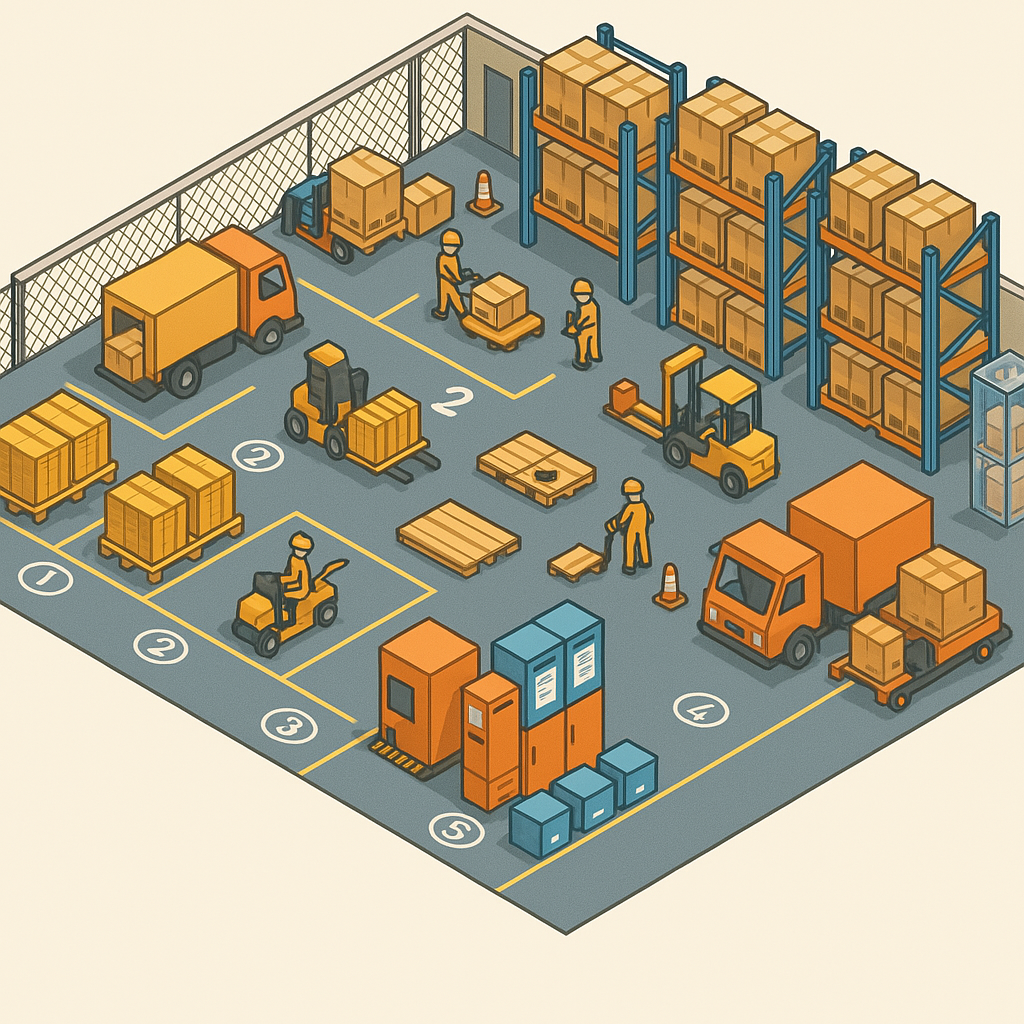
Like many industries, the material handling and warehouse storage sector is undergoing a major transformation. With an increasing demand for productivity, sustainability, and efficiency, racking systems are evolving rapidly. Businesses that embrace cutting-edge technologies will be better positioned to streamline operations and stay competitive.
At Pac Rac Systems, we believe the following trends will shape the future of warehouse racking and storage solutions in the coming years.
1. Automated Racking: Robotics & AI Integration
Warehouse automation is redefining how logistics professionals approach storage. Automated racking systems, powered by AI and robotics, are still very new but are being adopted at an accelerating pace. These systems use robotic arms, conveyors, and automated guided vehicles (AGVs) to handle inventory with minimal human input.
The benefits are compelling:
● Faster storage and retrieval
● Real-time inventory tracking
● Reduced labor costs
● Higher storage density
As businesses seek ways to increase output and reduce overhead, automation is proving to be a game-changer in warehouse racking design.
2. Smart Tech with IoT Integration
The rise of IoT (Internet of Things) is ushering in the era of smart racking systems. Sensors embedded into racking structures now monitor inventory levels, track usage, and even predict maintenance needs.
Key benefits include:
● Minimized stock shortages
● Fewer picking and packing errors
● Enhanced space utilization through data insights
IoT-enabled racking systems reduce human error while improving accuracy and operational efficiency. These “smart racks” are ideal for businesses looking to make data-driven decisions and maintain full visibility of their warehouse in real time.
3. Modular & Adjustable Racking Systems
Today’s warehouses need to be agile. Modular and adjustable racking systems offer the flexibility required to adapt to changing inventory profiles or seasonal product rotations.
Features include:
● Customizable beam heights
● Tool-free reconfiguration
● Minimal disruption to daily operations
Some emerging systems even include autonomous mobile platforms that move entire shelving units on command — giving warehouse managers the ability to reorganize floor plans in hours, not days.
4. 3D Printing for Custom Components
While still emerging, 3D printing technology is set to disrupt racking component manufacturing. Warehouses can now print their own parts — including brackets, connectors, and custom mounts — without relying on external suppliers.
Advantages of 3D-printed racking parts:
● Faster turnaround times
● Reduced shipping and lead time
● Lower prototyping costs
For large-scale operations, having a 3D printer onsite means a near-instant solution for replacement parts across all warehouse storage systems.
5. Vertical and High-Density Storage Solutions
With warehouse rental and real estate prices climbing, maximizing vertical space has become a top priority. High-density storage options such as mobile pallet racking and shuttle racking systems create the ability for businesses to increase capacity without expanding their physical footprint.
These systems:
● Reduce aisle space
● Utilize vertical height more efficiently
● Provide scalable growth without relocation
For companies facing space constraints, high-density racking is one of the most cost-effective storage upgrades available today.